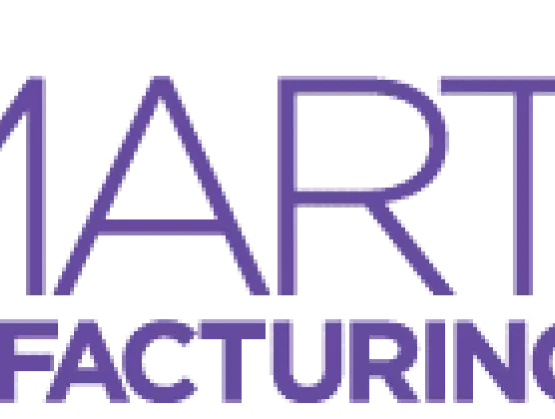
OSAT (アセンブリおよびテスト外部委託業者)は現在、世界の半導体産業のアセンブリおよびテスト工程製造の大部分を担っています。OSATの工場では、手動操作がレガシーです。意思決定は手動操作によるもので、材料やWIP(仕掛品)を移動させるのも手動です。工場では、事実上すべてが手動操作で行われています。さらに、OSATの工場環境は、典型的には、装置のレイアウト、材料キャリアおよび保管について、物理的な制約が数多く存在します。工場におけるマテリアル・ハンドリングを自動化するためには、このような制約の全てが課題となります。
また、IDMと比較した場合、OSATにおける売り上げ利益率および営業利益率はとても低いものですが、OSATが世界中で扱う半導体製品の割合は年々増えており、一方IDMのシェアは減少しています。生産量の増加と利益率の低さから、OSAT工場では自動化が進められていますが、克服すべき課題も多く存在します。
山積する技術的課題
OSATでは、生産の自動化にあたり、多くの技術的な課題に直面しています。まず、工場にすでにあるレガシー装置は、通常25年から30年も前から使われているものです。これら古い装置は、自動マテリアルハンドラーに対応するように設計されていません。例えば、古い装置のアクセスドアは、装置を大幅に改良しない限り、自動化されたWIPの受け渡しの実現は困難ということになります。
第2に、OSATの工場には自動化を支えるためのインフラが整備されていません。まず、これらの古い装置のほとんどはSECS/GEMに準拠していません。(SECS/GEMは、装置からホストへのデータ通信のための半導体業界の標準装置インタフェースプロトコルです)。したがって、これらの機能を、既存の装置に後付けするか、装置から必要なデータを抽出する他の手段(例えば、装置の制御を行うPLCからデータを取得する)が必要となります。
同様に、現在使用されているWIPキャリア(ウエハキャリア、トレイ、マガジンなど)は、自動化対応の設計ではありません。半導体ウェーハ製造とは対照的に、ほとんどのOSAT企業は、キャリアの在り方について異なる考え方を持っているようです。特に、半導体工場内でウェーハをある装置から次の装置へ運ぶために使われる、標準的な300mmFOUP(Front Opening Unified Pod)のようなものはありません。OSATの領域では、キャリアの形状、構成、さらにはグリップハンドルのバリエーションの多さが工場の自動化を妨げています。このように、さまざまなキャリアすべてに適応可能なグリッパー(grippers)と柔軟性を備えたマテリアルハンドリングロボット(搬送ロボット)をどのように設計するか?それは、難しい問題であり、高額な費用が必要となります。
OSATの施設自体は、単純に自動化が考慮されなかった時期に設計されたことから、自動化された搬送ではなく、作業員による搬送をベースに設計されています。その結果、図1に示すように、これらの施設の装置は非常に密接に設置されています。(フロア・スペースのコストを削減するため)。
図1:テスト施設内における装置の密接な配置は
自動マテリアルハンドリング採用を妨げている
OSATの工場では、半導体ウェーハ製造工場でよく行われているような、自動運搬装置を床にあるいは天井に、新たに設置することはとても難しい状況です。AGV(無人搬送車)がOSATのレガシー工場内で稼働することはありません。なぜなら、AGVが走行する余裕がないからです。
課題への取り組み
では、これらすべての課題に対処するにはどうすればよいのでしょうか?まず、工場内で行われる作業の性質を理解する必要があります。これまで述べてきたように、これらの動作のほとんどは、現在、手動で行われています。すべての決定とマテリアの搬送は作業員により行われているです。
完全な手動操作から完全な自動操作へと一足飛びに移行する方法はありません。なすべきことが多すぎます。意思決定の自動化が可能となるレベルに到達するためには、膨大な作業が必要となります。このようなレベルの自動化を実現するには、主要システムの搭載が必須です。
25年ほど前、多くの企業がOSATの工場におけるアセンブリやテストの自動化に取り組みましたが、うまくいきませんでした。稼働中の装置から必要なデータの抽出することができず、適切な意思決定に必要なデータがなかったことが原因です。あまりにも多くの必要とされるシステムが欠如していました。例えば、AGVを追加する場合、1人あるは2人のオペレータが一台のAGVとともに移動しながら、AGVに指示を出さなければなりませんでした。このような場合、自動化によるメリットはまったくありませんでした。当時、自動化に成功する方法はありませんでした。
スタンダードの必要性
OSAT工場では、アセンブリおよびテスト自動化を実現するための障害のひとつに、キャリア、ロボット、レイアウトおよび設備に関するスタンダードの欠如が挙げられます。前工程に関するスタンダードは数多く存在します。半導体製造工場の前工程向けに開発されたSEMI-E82、SEMI-E84、およびSEMI-E88を適用する場合がありますが、それらをOSATにおける後工程施設の要件に適合させる必要があります。そして、OSATには、新たなスタンダードを必要とする特別な要求もあります。このことは、SEMIおよび業界企業に、とってまさにチャンスであると言えます。
アセンブリおよびテストの完全自動化のためのアーキテクチャは、図2に示すように、4つの層を含んでいます。
図2:組み立てとテストの完全自動化に含まれる4つのレイヤー
完全に自動化された施設には、図2の上部にあるデータレイヤーから始めて、スマートな(高性能な)スケジューリングとディスパッチ(割当て)の決定に必要な、すべてのデータを提供できるデータベースシステムを、備える必要があります。次に、これらのデータベースは、ロジック層において、スマートで(高性能で)自動化されたスケジューリングおよびディスパッチ・アプリケーションに情報を提供します。そして、スケジューリング・アプリケーションおよびディスパッチ・アプリケーションは、制御コマンドを制御層内の自動搬送およびマテリアル・コントローラ、および自動装置ハンドラに情報を送ります。
このすべての自動化を行うには、図の先頭から始めなければなりません。自動化された装置および装置コントローラは、スケジューリング・アプリケーションおよびディスパッチ・アプリケーションからのコマンドを必要とし、その次に、データベースからのデータを必要とします。それによって、スマートな決定を行うことができるようになります。つまり、完全自動化への出発点となるのは、データ層と、この層にデータを供給するシステムです。
最適な設備ワークフローを作り上げるためには、大量のシミュレーションが必要です。これらのシミュレーションは、データベースから抽出されたデータによって実行されます。自動化において無視されがちな側面の1つに、バックアップ計画の必要性が挙げられます。たとえば、AGVで障害が発生し、スケジュール通りにマテリアルを搬送できない場合のバックアップ計画はどのようなものでしょうか。シミュレーションは、このようなイベントの緊急時対応計画の作成に役立ちます。
ケース・スタディー
アプライドマテリアルズ(Applied Materials)は、完全自動化の導入において、組立工場およびテスト工場と協力してきました。この目的にむけて、工場は自動化を可能にするための多くの改良(物理的なおよびシステム的な)に取り組んできました。例えば、ダイボンダー装置は、AGVが装置にマテリアルをロードし、作業が完了したマテリアルを取り出せるように、すべての機器のドアを取り外して、自動化に対応するよう改造されました。さらに改良し、ダイボンダー装置への出し入れに複数のマガジンを取り付けることで、装置間の作業フローを円滑にするバッファの提供を可能にしました。そして、WIPの受け渡しの決定を支援するために、単純な計装とネットワークがマシンに追加されました。
これらの装置改良は、この特定装置のボトルネックのみに対する対処でしたが、そのような単純な改良でさえ、マガジンまたはトレイのミスアライメンといった手動操作によるエラーの発生を減らすことに役立ちました。また、このような変更により、オペレーター(人)の介在の必要性が減り、その結果、装置の運転コストを抑えることにつながります。このような自動化機能の段階的な強化は、ここ数年、最先端の企業によって実施されてきました。
まとめ
アセンブリおよびテストの完全自動化の導入は実現可能であるだけでなく、将来の収益性のためにも必要です。OSATは、製造ミスを減らし、品質を向上させることによって、製造量の増加と利益率の低下という課題に対処しなければなりません。(品質要求は自動車産業によってますます高まります。)先駆的な取り組みによって、アセンブリ・テストの製造ラインは自動化できることが明らかになってきました。
IDMには製造自動化の長い歴史がありますが、OSATは世界中の製造量のシェアが高まっていることから、現在、同様の道を歩んでいます。その過程で、OSAT関係者は彼らの経験と独自のニーズに合わせた新しいスタンダードを開発する必要があります。
Shekar Krishnaswamy氏は、アプライドマテリアルズ(Applied Materials)のシニアマネージャで、FA製品およびソリューションのビジネス開発およびプリ・セールスを担当しています。そして、ウェーハ製造、バンプ、アセンブリおよびテストを含む半導体製造のあらゆる分野で27年以上にわたる経験を有しています。専門分野は、典型的工業技術手法およびモデリング、スケジューリング、ディスパッチ、FAなどのシステム関連の手法です。Krishnaswamy氏は、アプライドマテリアルズ(Applied Materials)の前は、IBM、Motorola、およびAMDで、工場およびサービス・グループをサポートする運用研究部門の管理を含め、上級技術および管理の職に就いていました。
Krishnaswamy氏は機械工学の学士号および工業工学およびオペレーションズ・リサーチの修士号を有しています。
Note: SEMI Smart Manufacturing Technology Communityについては こちらをクリックしてください。
本件についての問合せ:
SEMIジャパン コリンズ純子(jcollins@semi.org)
初出:2019年1月23日、Standards Watch
※本稿は、Standards Watchに掲載されました記事を日本語訳にしたものです。
元の記事 https://blog.semi.org/technology-trends/automated-material-handling-for-semiconductor-assembly-and-test