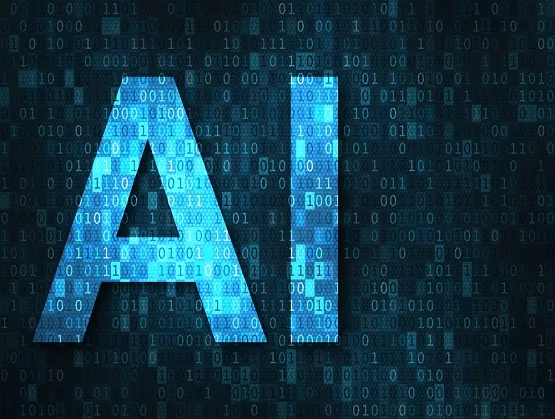
はじめに
電子機器製造の生産を自動化することで、高品質の製品を生産することができますが、人間が介入しないため、特定の故障につながる可能性があります。IIoT(産業用IoT)、ビッグデータ解析、クラウドコンピューティング、人工知能(AI)などの急速な技術進歩により、多くの製造工程のインテリジェント化が進み、インダストリー4.0も近い将来に実現する可能性がでてきました[1]。スマート製造では、オペレーショナルデータや検査データをベースにしたリアルタイムの意思決定がされ、製造工程全体がひとつのフレームワークに統合されます。この先、未来の製造工程は、デジタルのサイバーフィジカルシステムに転換し、高い効率性を確保すると同時に、あらゆる不確実な状況にプロアクティブに対応します。
表面実装組立ラインでは、IIoT技術によって機器の状態や品質データの収集ができます。従って、AIや機械学習アルゴリズムなどのデータ駆動型ソリューションを利用することで、異常な欠陥を診断し、生産中の予期せぬ変化や状況に対応して、装置パラメータを最適に調整することが可能です。ニューヨーク州立大学ビンガムトン校(通称ビンガムトン大学)の研究チームは、プリント基板組立にスマート製造ソリューションを導入し、歩留まりとスループットを改善するため、表面実装業界のさまざまなパートナーと協力して、AIベースのクローズドループフィードバック制御とパラメータ最適化を基盤とする斬新なフレームワークを開発しました。このAIベースのフレームワークによって、表面実装組立におけるデータ駆動型工程制御のロードマップが示される可能性があります。
表面実装組立における装置のAI化
表面実装組立の一つ一つの工程が、プリント基板製品の品質とスループットに大きく影響をします。とりわけ、はんだ印刷工程は、プリント基板のはんだ不良の60%がこの工程に起因するため、非常に重要となります。プリント基板のパッドのひとつでも、十分な量のはんだペーストが塗布されないと印刷不良となり、プリント基板のリワークとリペアのコストが発生します。ピック&プレース工程は、高額の装置への投資、長い工程時間など、最もコストがかかる部分です。はんだリフロー工程では、リフロー炉の温度他の設定がはんだ接合の品質と信頼性を左右します。このため、はんだペースト検査(SPI)、自動光学検査(AOI)等の複数の検査装置が表面実装組立工程で使用されています。特にAOIは、はんだリフローの前後の部品不良の検出するために、2台の装置が使用される場合があります。
多くの電子部品が小型化し、表面実装の組立工程に起因する不良が増加しています。ビンガムトン大学の電子機器スマート製造研究所(SEML)は、2台のはんだペースト印刷機、2台のチップマウンター、1台のリフロー炉に加え、SPIおよびAOI装置を完備しています。研究チームは、SEMLでこれまで8,000枚以上のプリント基板をテストしました。その結果、物理的特性に基づく数値手法だけでは、小型部品の挙動の説明することには、実際上、限界がある可能性が判明しました。温度や湿度といった未知の環境要因、装置の較正、測定精度、振動などが、表面実装組立の生産の質に影響を与えているかもしれません。しかし、最近の研究では、AIを用いた手法によって、従来のアプローチよりも、製品品質が最大35%改善し、スクラップ率が低減し、半導体製造におけるファブオペレーションを最適化できることを示しています[2]。これは、データ駆動型のインテリジェントな工程制御によって、表面実装組立工程が進化する可能性を示唆しています。
表面実装組立のスマート化の目標は、オフラインとオンラインの双方のシナリオで、設定の最適化を維持することにあります。AIとデータ解析によるソリューションは、全ての表面実装組立工程を、生産前にはオフライン制御で、生産中はオンライン制御で最適化することが可能です。AIベースのクローズドループフィードバック制御の全体図を図2に示します。
表面実装組立AIモジュール
はんだ印刷工程では、4つのAIモジュールで構成されています。
- 印刷アドバイシングモジュール(PAM)
- 印刷最適化モジュール(POM)
- 印刷診断モジュール(PDM)
- メタルマスク洗浄工程制御(CPC)
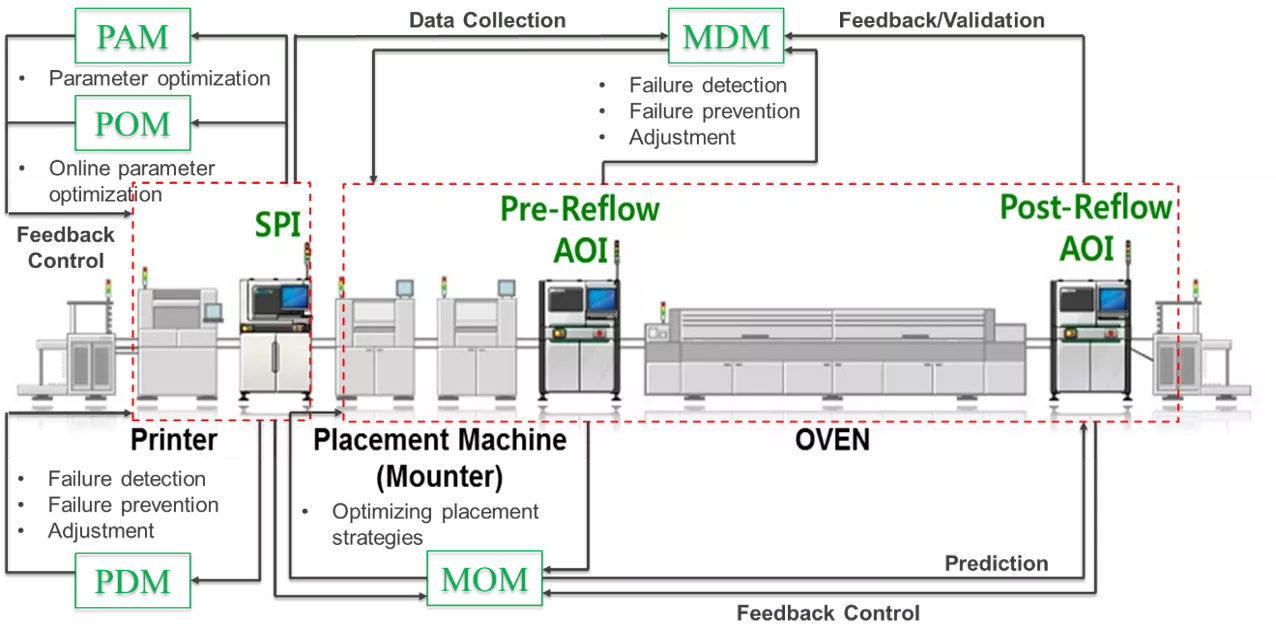
図2:AIベースのクローズドループフィードバックプラットホームの模式図
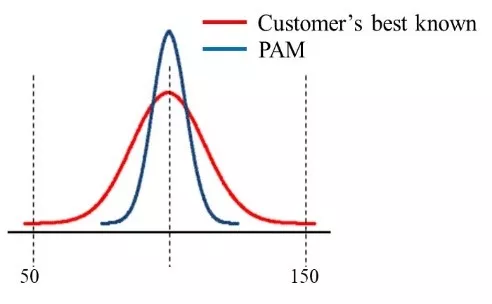
図3:カスタマの最も良く知られた印刷パラメータに対するPAMの有効性
PAMの目的は印刷機の重要パラメータの理想的な初期設定を、ハイブリット機械学習とヒューリスティックな最適化によって推奨することです[3]。これには、印刷速度、印刷圧力、セパレーション速度などがあります。ケーススタディとして、研究チームは自動プリント基板テストベッドを使い、最も良く知られた印刷パラメータ設定とPAMによる設定の印刷結果を比較しました。実験結果は、PAMの方が工程能力指数(Cpk)を50%上回ることができることを示しました(図3)。
POMは、印刷品質をモニタリングし、動的な条件に適応するためにオフセット値および工程パラメータを微調整することで、印刷パラメータをリアルタイムに最適化します[4]。実験の結果、POMの印刷パラメータ調整により、オフライン制御と比較してCpk値で30%以上の生産品質向上を達成しました。PDMは、工程品質を向上させ、ダウンタイムを削減するために、潜在的な印刷障害の異常検出と診断を行います[5]。実験結果によると、PDM は、基板サポート、スキージ、ペースト条件などの不適切な印刷機のハードウェア問題を 87% 以上の精度で予測することができました。CPCは、図4に示すように、SPIの情報を使用して、メタルマスク下面の残留物の蓄積レベルを推定し、メタルマスクの適切な洗浄プロファイルとサイクルを決定します[6]。CPCを導入すると、生産ラインで使用されている既知の洗浄パラメータと比較して、印刷品質の安定性が34%、Cpkが10%向上することが期待できます。
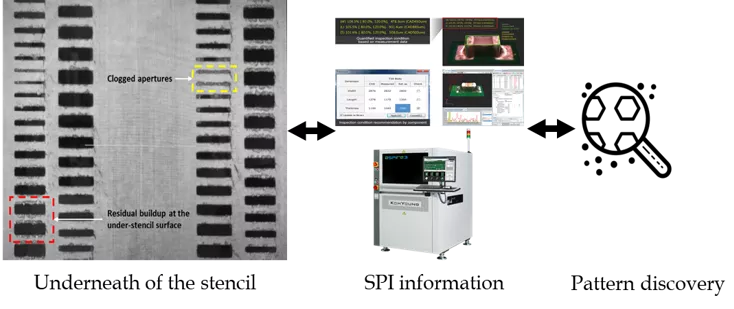
図4:メタルマスク洗浄制御のための残留物堆積予測
ピック&プレース工程では、マウンター装置のパラメータの最適化に加えて、マウンター最適化モジュール(MOM)とマウンター診断モジュール(MDM)を装置自動化工程として利用することができます。MOMは、セルフアライメント効果を適切に利用することで、図2に示すように、SPI装置、リフロー前AOI装置、リフロー後AOI装置で収集したデータをもとに、部品のリフロー後の位置を予測して最適な配置を決定します。また、MOMは、生産中にも変化に適応した配置位置を提供します。MOMのフレームワークでは、まず、はんだペーストのオフセット情報に基づいて、複数のダイナミックな配置オプションが生成されます。部品のX方向とY方向の最終的なオフセットは、K近傍法回帰モデルと勾配ブースティング回帰モデルを重ね合わせたハイブリッドAIモデルによって予測され、リフロー後のずれが最小となる最適な配置が、MOMによって特定されます。
実験の結果、MOMは従来のP&P配置方法(パッドセンターに部品を配置する方法)と比較して、最終的なずれを18%減少させることができることがわかりました。MDMは、P&P装置のオペレーショナルデータとAOI検査データを用いて、P&P不良の根本原因にさかのぼり、将来の故障を予防する予知保全手法です。MDMでは、不適切なノズルサイズ、部品の汚染、フィーダーの問題など、欠陥の既知の根本原因を84.50%の精度で特定することができます。これは、AIベースの診断アルゴリズムによって異常が検出された場合、複数の異なる実装不良を自動的に検出・分類できることを意味します。
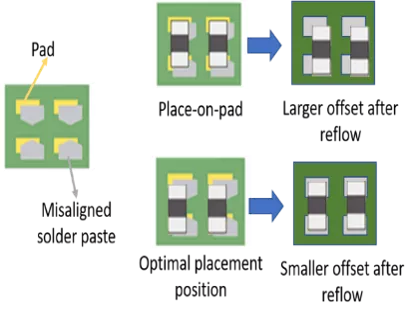
図5:MOMによる最適な配置
リフロー炉で対策が必要な課題のひとつに、リフロー炉温度の最適な設定を見つけることがあります。これはプリント基板製品の最終的な品質に影響します。はんだペーストメーカーは、はんだペーストの組成の物理的特性に基づいたターゲットプロファイルを通常は提供しますので、これと一致するはんだ接合部の温度が必要となります。それゆえ、リフロー技術者は、接合部の温度プロファイルがターゲットプロファイルと正しく一致するように、マニュアルでリフロー炉の温度を微調整しなければなりません。これには相当のコストと労力が必要です。研究チームは、プリント基板の熱プロファイルとそのレシピに基づいた、自動リフローレシピ最適化モデルを提案しています。
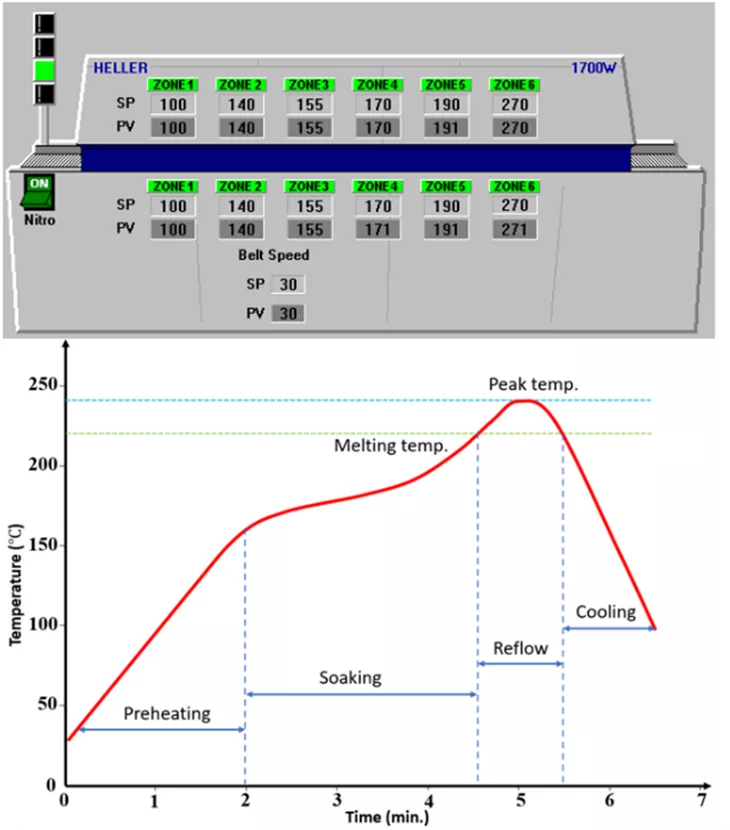
図6:温度レシピと温度プロファイルの最適化
まず、当初のレシピで予測モデル用のデータを収集し、熱プロファイルとレシピの関係を明らかにします。次に、レシピに基づいて熱プロファイルを予測するAIベースのモデルを開発します。従来の手法と異なり、AIベースの手法では、予測された温度と与えられたプロファイルのギャップが最小となる最適なリフロー炉のレシピを生成します。その結果、AIベースの予測モデルでは、1時間以内の処理時間で、与えられたプロファイルの温度曲線に対する適合率が97%になるなど、有望な結果を得ることができました。提案されたモデルは、時間、労力、材料の節約といった大きな利点が他にもあります。こうして、プリント基板のリフロープロセスの自動化度合いが高まります。将来的には、複数の検査装置からのデータを統合して、リフロー最適化プロセスを完全に自動化し、より信頼性の高い結果を得られるようにする予定です。
まとめと結論
小型の電子機器製品は、プリント基板製品の品質を高めるために、表面実装組立工程が複雑化しており、多くの不確実要素があるため、表面実装組立プロセスの理論的解釈が困難になっています。AIと各種検査から収集されたビッグデータを活用することで、表面実装組立工程はインテリジェント化し、動的な環境状況に柔軟に対応できるようになります。表面実装組立工程全体で最適な制御パラメータを維持することで、設計されたスループットを維持しつつ、最終的なプリント基板製品の品質を向上させることができます。自動化されたスマートシステムは、次のレベルのエレクトロニクス製造の道を切り開きます。エッジ/クラウドコンピューティングを通じてエンドユーザーからのデータや情報を活用し、多品種/少量生産の効率を高めてカスタマイズされた製品の製造を高速化します。また、設計の多様性を高め、納期を短縮することができます。
著者について
Sang Won Yoon教授は、2019年にSUNY Chancellor's Award for Excellence in Scholarship and Creative Activitiesの受賞者であり、多くの生産性の高い長期的な産業界とのコラボレーションをリードする、優れた功績のある研究者です。Yoon教授は、パデュー大学生産工学部で博士号を取得した後、2010年にニューヨーク州立大学ビンガムトン校のシステム科学・生産工学部のワトソン・スクールの教授に就任しました。 2010年にニューヨーク州立大学ビンガムトン校システム科学・産業工学科ワトソン・スクールの教授に就任しました。
Yoon教授の研究は、統計的学習手法を用いて大規模データセットをより良く理解することに留まらず、最適化、ソフトコンピューティング、シミュレーション、および従来の機械学習アルゴリズムを用いた複雑な理論を活用しています。その結果、ユン教授は130以上の国際的学術誌や会議録に論文を発表しています。また、データサイエンスの学際領域(TAE)のメンバーであり、現在は健康科学のTAEのメンバーとして活躍しています。
著者は本稿の執筆にあたり、以下の方々にご協力いただきました:
- Daehan Won, dhwon@binghamton.edu, Assistant professor
- Jingxi He, jhe56@binghamton.edu, Ph.D. candidate
- Shrouq M. Alelaumi, salelau1@binghamton.edu, Ph.D. candidate
- Yuanyuan Li, yli352@binghamton.edu, Ph.D. candidate
- Yuqiao Cen, ycen2@binghamton.edu, Ph.D. candidate
参考文献
[1] Qi, Q., and Tao, F., 2018. Digital twin and big data towards smart manufacturing and industry 4.0: 360 degree comparison. IEEE Access, 6, pp.3585-3593.
[2] 10 Ways machine learning is revolutionizing manufacturing in 2019. https://www.forbes.com/sites/louiscolumbus/2019/08/11/10-ways-machine-learning-is-revolutionizing-manufacturing-in-2019/?sh=7cd2e9e22b40.
[3] Khader, N. and Yoon, S.W., 2018. Stencil printing process optimization to control solder paste volume transfer efficiency. IEEE Transactions on Components, Packaging and Manufacturing Technology, 8(9), pp.1686-1694.
[4] Lu, H., Wang, H., Yoon, S.W. and Won, D., 2019. Real-Time stencil printing optimization using a hybrid multi-layer online sequential extreme learning and evolutionary search approach. IEEE Transactions on Components, Packaging and Manufacturing Technology, 9(12), pp.2490-2498.
[5] Alelaumi, S., Wang, H., Lu, H. and Yoon, S.W., 2020. A Predictive Abnormality Detection Model Using Ensemble Learning in Stencil Printing Process. IEEE Transactions on Components, Packaging and Manufacturing Technology, 10(9), pp.1560-1568.
[6] Alelaumi, S., Khader, N., He, J., Lam, S. and Yoon, S.W., 2021. Residue buildup predictive modeling for stencil cleaning profile decision-making using recurrent neural network. Robotics and Computer-Integrated Manufacturing, 68, p.102041.