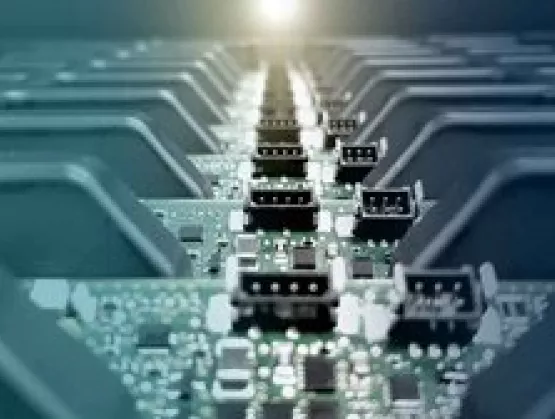
生産コストは、通常と人件費と材料費がベースとなり、これによって製造経費が決まります。しかし、このアプローチは十分に正確でしょうか。生産における品質不良や効率の欠如のコストはどうでしょうか。パンデミックは半導体製造にどのような影響を与えているのでしょうか。そして今後何が期待できるでしょうか。
SEMIはこのほど、QualityLine社の創業者兼CEOであるEyal Kaufman博士に、製造管理と製品の品質と歩留まりを向上させるための最適なデータソースについてお話を伺いました。同社は、イスラエルのキルヤット・ガトに本社を置くスマート・マニュファクチャリングの分析ソリューションを提供する企業です。Kaufman氏から、コストを削減しながら製造効率と製品品質を向上させるために同社が採用しているベストプラクティスの要点をお聞きできました。また、COVID-19パンデミックが半導体のスマート・マニュファクチャリングに与える影響や、AIが工場の労働者の安全を守るためにどのように役立つかについても説明いただきました。
スマート・マニュファクチャリングについて、さらに洞察を深めるには、10月20日~22日に開催される「SEMI Global Smart Manufacturing Conference」にご参加ください。参加申し込みはこちらです。
SEMI:実際の製造コストは、生産不良品、修理品、返品、部品のスクラップや遅配などさまざまな要素から計算されます。製造業における品質と効率の欠如は、ビジネスを蝕む可能性があります。企業がこれらの課題を克服するために、どのような支援をしているのでしょうか?
Kaufman氏:利益率を高めるためには、非効率な部分を特定し、優先すべき改善を決めることが重要です。製造品質と効率の不足が測定されたなら、製造データを継続的に収集して最終的なコスト分析を実行し、その分析結果を製造プロセスの改善に活用します。
スマート・マニュファクチャリングにより、自動化された工場の異常を検知し、生産性を向上させ、収益性を向上させることが可能になります。現在では、自動化データが、工場内のあらゆる製造装置や試験装置から収集されています。しかし、多くの産業では製造データの収集がいまだにマニュアルで行われており、時間と工数の多額の経費がかかっています。リアルタイム分析システムの場合は、自動的にすべてのソースからデータを自動的に収集し、分析に関係するものを選択しますから、品質と効率の不足を測定し解決するための、最も正確で効果的な方法となります。
スマート・マニュファクチャリングのデータ駆動型決定は、コストの低減と製造戦略の改善をもたらし、工場オペレータが製品品質を向上することを可能にし、生産能力を引き上げ、製造性を最適化する製品設計を実現します。分析システムは、製造現場のオペレーションをモニタリングし、ベンダーやサブコンの製品基準を参照して、根本原因分析を実行します。これらのデータはすべて、不良品返品率を低減し、投資収益率を加速させます。これが、スマートな製造技術が必要な理由です。
SEMI:製造工程で蓄積されるデータには、故障、規格外れ、装置の有用性などの重要な情報があります。最適な分析システムを構築するためには、どのようなデータが必要なのでしょうか?
Kaufman氏:今日、多くの企業がデータマッピングを実行して、データキャプチャを自動作成しています。こうした企業では、テストデータやセンサーデータ、製品設計データを使用する必要があるのか、顧客やベンダーからのフィードバックを収集する必要があるのか、と悩むことがよくあります。効果的な製造分析システムを構築には、次のようなデータソースを使用すると良いでしょう:
- 顧客からのフィードバック(返品、苦情など)
- 自動試験装置と手動試験活動からの試験データ
- 故障したユニットを修理した技術者からのフィードバック
- ベンダーが行うテストプロセスの分析
- センサーデータ
- 当社のERP/MESシステムからのデータ
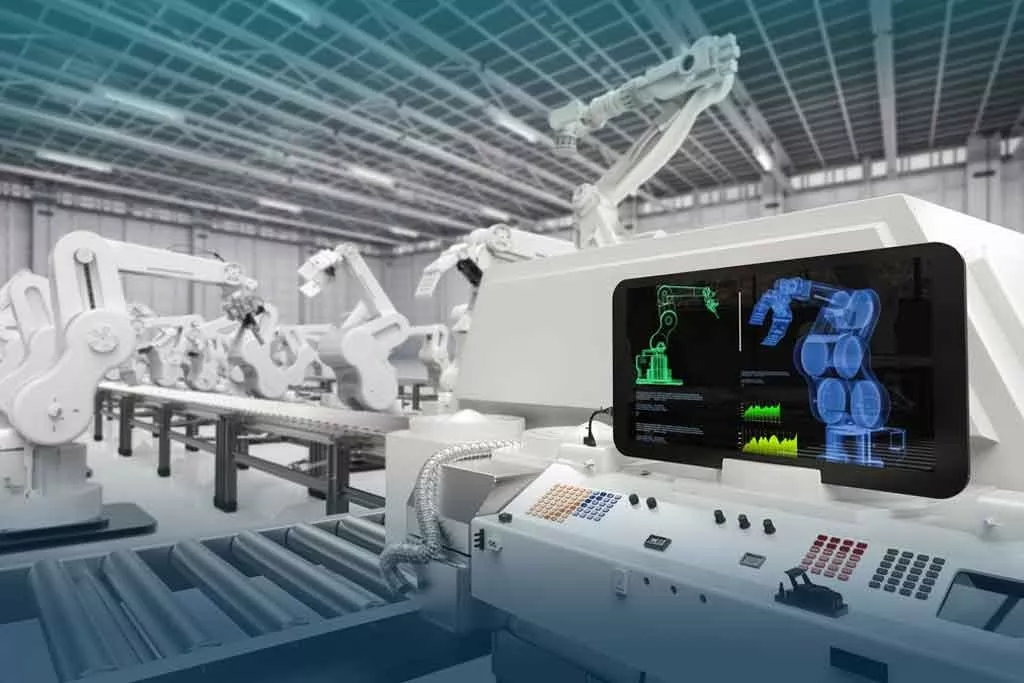
AIは、蓄積されたデータを含め、あらゆるタイプやサイズのデータ構造を自動的に統合して解釈することができます。また、AIによる分析は、各製造ステージ間の相関関係も明らかにし、工場のオペレータは、既存のプロセス、装置、データ出力を変更することなく、深層診断や根本原因分析をすぐに実行して、問題の解決と予防を図ることができます。機械学習は、工場がどのようにデータベース運用しているかを評価し、生成されたすべての情報を分析システムに入力して、工場の効率を継続的に改善するためのノウハウを提供します。
SEMI:製造品質と歩留まりを改善するために、どのようにデータソースを選択すればよいのでしょうか。
Kaufman氏:製造工程で蓄積されたデータの正確性と完全性が、製造コストを低減しながら歩留まりと品質を向上させるための鍵となります。スマート・マニュファクチャリングとは、デジタルやリモートで接続された装置を使用することで、生産プロセスを監視するテクノロジー主導のアプローチです。その目的は、製造プロセスの異常を特定し、分析を活用してプロセスの歩留まりと製品の品質を向上させることにあります。
該当するデータを選定するために、実際の製造セルの効率化につながる各種、各ソースのデータを収集します:
- 自動試験装置のテストデータ
- マニュアル試験のテストデータ
- 修理プロセスの分析(製造プロセスでの故障、顧客からの返品)
データ構造を収集したら、次にこれを製造プロセスで実行可能な情報に変換します。QualityLineスマート・マニュファクチャリング・ソリューションは、ワンストップであらゆる製造データ構造を解釈することができます。当社の高度な製造分析システムは、品質と歩留まりの異常を検出して生産ラインの非効率性を明らかにし、製造品質と効率を改善する機会を提供します。
SEMI:QualityLineのアプローチを説明いただけますか。
Kaufman氏: 製造業におけるインダストリー4.0は、第4世代の産業革命であると主張しています。製造インテリジェンスや機械学習などの先進技術により、製造ラインでの不良ゼロを効率的に実現することができます。デジタル工場では、以下のような技術や手法が活用されています:
- ビッグデータ
- 自己最適化
- 自己設定
- 自己診断
- コグニティブ学習と機械学習
スマート・マニュファクチャリング技術は、リアルタイムでデータを継続的に収集・分析することにより製造プロセスを強化し、高い品質性能を実現し維持します。無駄や非効率を削減しながら、効率と歩留まりを大幅に向上させることが目標です、
これまで、保存されたすべての製造データを統一データベースに統合する現実的な方法はありませんでした。QualityLineの高度な製造分析を利用することで、どのような工場でも新たなハードウェアをインストールすることなくデジタル化が可能になります。ハードウェアの追加にはコストがかかり、既存のデータを広範囲に統合するだけでなく、トレーニングへの投資も必要になります。
当社のユーザーフレンドリーなソリューションは、自動化が全くされていない産業についても製造データの統合をサポートします。まず、あらゆる種類のマニュアル試験からデータを収集して分析し、それを製造分析に統合することで効率向上を図ります。
SEMI: 合否判定基準だけでは製造歩留まりや品質を管理する上で不十分なのはなぜですか?
Kaufman氏:大量生産プロセスの管理は、製品が出荷されるまでに何百ものタスクを成功させる必要があり、容易なことではありません。当社は、原材料の入荷から顧客に完成品を納入する前の最終段階まで、生産フローの各段階でテストプロセスを確立します。予期せぬダウンタイム、廃棄品、不良品を防ぐために、あらゆるタイプの関連データを収集・解釈し、有意義な情報に変換し、以下のような機能を設定します:
- 各製品ユニット、各プロセス、そして工場の試験データやプロセスデータの収集と解釈
- 品質・歩留まり問題の自動検出
- 正確で迅速な根本原因分析プロセス
- 異常が発生した場合の自動アラート
- 予測プロセスの可能性と失敗のレベル
- 主要パフォーマンス指標の測定
多くのメーカーでは、各パラメータのテスト基準を合否という単一の指標に置いています。テスト結果が合格を示した場合、そのユニットは次の製造ステージに進む準備ができています。テスト結果が不合格を示した場合、ユニットはさらなる分析のために技術者に送られます。
製品品質の単純な合否判定基準では、対象ユニットの技術的パラメータの1つ以上が許容範囲内に収まっているエッジケースに関する情報がほとんど、あるいは全く得られないため、到底十分とは言えません。エッジケースは、極端な環境(寒さ、熱、湿度、電気的過負荷、衝撃など)での運転中にユニットの故障につながる可能性があります。実際には、大量生産ラインでは、テストステーションから収集した詳細情報をすべて継続的に消化することは不可能です。データは、重要な品質問題が発生し、根本原因を理解するためにさらなる分析が必要な場合にのみ、詳細に分析されます。
情報が処理能力を上回り、重要なパラメータが見過ごされては、プロセスを制御し品質と歩留まりを向上させることはで困難です。新しい技術では、高速でスケーラブルなデータ統合が可能になり、リアルタイムでデータを収集して品質問題を早期に検出し、複雑なプロセスの乱れを特定して納期遅延を回避し、顧客に最高の製品を提供できるようになりました。データを実行可能な情報として正確に分析できてはじめて、工場のオペレータは製造品質プロセスを制御することができます。
SEMI:COVID-19はスマート・マニュファクチャリング市場にどのような影響を与えましたか?また、貴社の技術は工場のオンライン化をどのように支援してきましたか?
Kaufman氏:スマート・マニュファクチャリングは、労働力の減少、ソーシャルディスタンス、特定の製品の売上減少、業務コストの厳しい削減圧力といった、COVID-19の諸問題を克服するための支援を製造業者に提供する重要な役割を果たしています。
製造業のリーダーは、限られた労働力と稼働時間で効率的な工場運営を維持するという課題の解決策を、当社に求めています。少ない人員で工場の注文を満たすのは大変です。デジタルファクトリーテクノロジーは、オペレーションの遠隔監視を可能にし、効率性と能力を高めます。当社は、お客様がコストを削減しながら効率を向上できるよう支援をしています。
当社のリモート・モニタリング技術は、安全上の制約から工場に物理的に出向くことができない現場マネージャーや技術チームに、運用上の可視性を提供することができます。当社の高度な製造分析により、製造プロセス全域をモニターすることができ、生産ラインに発生する問題をリモート診断して解決することができます。
この重要な時期に、リモート・モニタリング・ソリューションを改善し、業界がパンデミックを乗り切る助けとなれることを誇りに思っています。当社の顧客の中には、そうでなければ工場を閉鎖していた企業もあります。私たちは、これまで自動化されていなかった工場の製造データを統合して、高い自動化レベルを推進してきました。顧客のプロトコルや自動化レベルに関係なく、既存の工場データとプロセスを統合することは、当社の大きな技術的優位性です。
SEMI:COVID-19の後、製造業とそのサプライチェーンはどうなるのでしょうか?
Kaufman氏:スマート・マニュファクチャリングは、現在では必須となっています。データを収集・分析して品質を向上させるだけでなく、顧客の不良製品の返品を50%削減し、廃棄物を22%削減しており、このどちらもが重要なポイントです。製造業の課題は今後もテクノロジーの進歩を加速させ、リアルタイムのデータ分析や人工知能(AI)を工場のオペレータに取り入れながら、効率性、安全性、生産性を向上させていくでしょう。
SEMI:サプライヤーは今後もスマート・マニュファクチャリング技術を追求していくのでしょうか。また、どのような成長機会がもたらされるのでしょうか。
Kaufman氏:はい、間違いなくそうです。COVID-19が機会と課題の両方をもたらすことで、業界はすでに変化しています。業界のリーダーたちは、突然の材料不足、需要の低下、労働者の不足など、新たなプレッシャーに直面しています。製造業にとっての成長の機会は、おそらくデジタル化にあるでしょう。これは、危機への即時対応がデジタル化によって進められたことでも明らかです。サプライチェーン全域の透明性、自動化、データ統合を高めるためには、インダストリー4.0のソリューションが欠かせません。QualityLineの製造分析は、主要な製造パフォーマンス指標を改善してきました。顧客からのフィードバックに基づいて、生産歩留まりを30%向上させ、何百万ドルも節約した顧客もいます。このような改善が、サプライヤーがパンデミックに耐えるために役立つのです。
QualityLineの創設者兼CEOであるEyal Kaufman博士は、25年以上にわたり、大手製造企業での事業開発、マーケティング、財務、オペレーション、エンジニアリング、品質管理の分野で、上級管理職としての経験を積んできました。QualityLineを設立する前は、Mobileye、Cardo Systems、Medisim Ltd.の副社長、OnTheGo SystemsのCEOを務めました。カリフォルニア・インターコンチネンタル大学で博士号、ニューヨーク市立大学でMBA、イスラエルのテクニオン大学で理学士号を取得しています。
SEMI SMART Manufacturing Initiativeは、スマート・マニュファクチャリングを通じた製品の品質、生産性、コストの最大化を実現するために、業界で認められたベスト・イン・クラスのプログラムやサービスを提供することに焦点を当て、スマート・マニュファクチャリングに対する認識と関心を高めるための世界的な取り組みです。活動内容は、マイクロエレクトロニクスのサプライチェーン全体でスマート・マニュファクチャリングを可能にするためのコア能力の構築に重点を置いています。
MADEin4は、半導体装置メーカーやシステム統合型計測器メーカーからRTOSや自動車産業などの主要アプリケーションまで、サプライチェーンの全範囲をつなぐ10カ国47社のパートナーによるコンソーシアムです。MADEin4プロジェクトは、半導体製造業におけるインダストリー4.0の大量生産をサポートするために、次世代の計測ツール、機械学習手法、アプリケーションを開発しています。