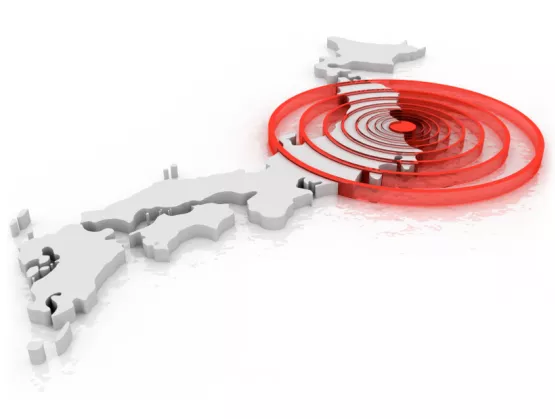
Wedged among four major tectonic plates, Japan is at the mercy of their abrupt herculean shifts and the earthquakes and tsunamis they can trigger. The fallout can be devastating. The magnitude 9 Great East Japan (Tohoku) temblor in 2011 and ensuing tsunami took nearly 20,000 lives, destroyed 138,000 buildings and cost $360 billion in economic damage.
Factories including silicon wafer production facilities owned by Shin-Etsu Chemical and MEMC Electronic Materials – together accounting for 25 percent of the global silicon wafer production – sustained heavy damage. Operations were suspended. The Kumamoto earthquake in 2016 also caused significant damage. The economic cost: as much as $7.5 billion.
With disaster risk rising on a global scale, these calamities offer valuable lessons in disaster preparedness and how companies can draw from their experiences to strengthen business continuity planning (BCP).
Earthquake experiences and lessons in BCP were the focus of the recent SEMI Japan Members Day as speakers from five semiconductor device and equipment manufacturers offered their BCP strategies to about 150 SEMI members. Following are key takeaways from their presentations.
Renesas: Create a robust production plant that is hard to break and easy to fix
Renesas Semiconductor Manufacturing’s Naka plant took about 80 days to resume production while its ability to deliver semiconductors was delayed even longer as it recovered from damage caused by the Tohoku earthquake, said Yoshiyuki Miyamoto, Representative Director and President at Renesas. Operations at the company’s Kawajiri plant were disrupted by the Kumamoto earthquake.
A key lesson from both earthquakes: The company needed to promote risk visualization from top-to-bottom in the supply chain. With the goal of making its plants easy to repair but hard to break down, Renesas implemented a risk management plan for earthquake preparedness plan to ensure stronger production line resistance and a stable supply to customers. The company ran simulations of multiple earthquake scenarios including aftershocks, enabling it to develop new BCP training and preparedness measures.
Sony: Staying transparent about the disaster, sharing and interacting with related companies
Yukihide Keigo, a representative from the Sony Semiconductor Manufacturing, showed footage taken the day the Kumamoto earthquake damaged a production line at its Kumamoto Technology Center. Sony is the top manufacturer of imaging sensors worldwide, and the Kumamoto plant is the backbone of that production. The magnitude of the foreshock fell within levels Sony had accounted for in its BCP at that time, and the line was expected to return to full production within a week. However, the magnitude of the earthquake that followed outstripped expectations, and the company’s BCP didn’t hold up. Three and a half months later, the plant had finally fully recovered.
The protracted recovery prompted Sony to develop an earthquake preparedness plan using a model that assumed double the magnitude of expectations. For full restoration, the company identified challenges to returning to full operation at each stage of the production line. Then it went even further, developing in-house diagnostics, implementing critical path methods and strengthening earthquake resistance of equipment that manages bottlenecks for the restart of the plant. The revision of its BCP plan led to the establishment of a system to shorten the resumption of production after a major earthquake to just two months.
Sony shared the contents of its BCP review with other companies to solicit help identifying any gaps and highlighted its partnership with Renesas in the Semiconductor Industry Association in Japan (JSIA), a committee of the Japan Electronics and Information Technology Industries Association (JEITA), to share materials procurement resources for the purposes of disaster preparedness and business continuity.
HORIBA STEC: Steady daily practices protect hundreds of millions of yen worth of products
HORIBA STEC’s Aso plant, near the epicenter of the Kumamoto earthquake, suffered heavy damage that cut off electricity and the water supply, yet production in its clean room resumed in just 10 days, said Hiroyuki Koyama, a factory manager at the plant. The plant’s quick recovery stemmed from daily preventive measures implemented before the quake such as connecting freestanding shelves for greater stability, applying thick rubber bands as rails to prevent manufactured goods from falling to the floor, and placing equipment on rolling carriages instead of fixed shelves.
The practices saved the Aso plant hundreds of millions of yen in products and materials that otherwise could have been lost in the earthquake. Koyama also offered the reminder that, with regulations governing factory layout and construction differing widely depending on factors such as a building’s age, companies need to tailor their BCPs to the unique characteristics of each building.
THK: The key point of dampening earthquakes
THK’s ACE Division develops earthquake dampening and vibration control devices designed to absorb the vibrational energy of an earthquake, though the devices must also be designed for precise analysis of that energy, said Hidemi Murao. Murao provided an overview of the latest technologies and products for dampening earthquake vibrations and shared test results from experimental devices.
Murao described how THK’s recently introduced Linear Motion (LM) Guide, an earthquake vibration dampening technology, can significantly reduce building vibrations during a temblor. In a video Murao showed to demonstrate how the guide works, a shelf loaded with equipment rests on a platform equipped with THK’s LM Guide equipment. Simulating an earthquake, the platform shakes vigorously in every direction but the shelf remains steady as the LM Guide dampens the vibrations. The platforms can be installed on floors or underground in buildings or factories to prevent shelves from toppling.
Tokyo Electron: The ideal BCP management system
One risk associated with BCP training is that it can become overly routine, dulling the response of employees in actual disasters, said Tokyo Electron Vice President Tatsuya Aso. To help keep its workers’ skills sharp, TEL held surprise drills with employees assigned to particular BCP roles to test their ability to adapt quickly to when disaster strikes. In addition, TEL has launched surveys in more than 70 overseas locations to optimize safety in these high-hazard facilities.
The SEMI Japan Members Day presentations made clear that the issue of BCP transcends boundaries between individuals, manufacturers, regions, and sectors within the global electronics supply chain. Disaster preparedness requires problem-solving across the entire supply chain, with companies sharing technical knowledge, offering mutual aid, and striving for continual improvement. Collaborative is essential.
At SEMICON Japan 2019, SEMI will continue to bring companies together to address BCP initiatives and share their technical knowledge with members.
Jim Hamajima is president of SEMI Japan.