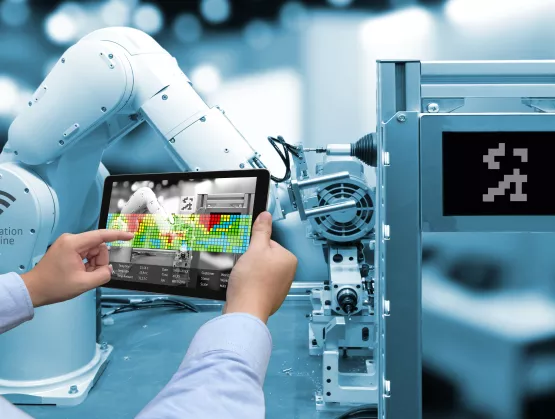
Part 2 of this two-part piece examines the potential benefits to be realized by pairing human Subject Matter Experts with smart silicon assistants, and what these new arrangements mean for semiconductor device manufacturing.
Part 1 explores best-practice perspectives on collecting and utilizing smart data in industries outside semiconductor manufacturing, one of the important takeaways from the Smart Manufacturing panel discussion at SEMI ASMC 2018.
So what does this observation (i.e. the field of medicine, in what seems at first glance a big data environment, is really just clusters and clusters of loose small data connected by the collective neural network of highly trained doctors and their colleagues) mean for semiconductor manufacturing?
We think it means we need to apply the same level of intense focus that we already devote to instrumented data collection and analytics in the fab to something more: we need to better capture the vast expertise of our engineering and operational talent in semiconductor manufacturing. We think we need to record what the subject matter experts (SMEs) in the fab see, hear, and think as they investigate yield excursions or machine-down problems.
We need to effectively combine product, process, equipment and component subject matter expertise / subject matter experts (SME) with big data analytics to more effectively solve manufacturing problems, be they killer or be they chronic. And we must provide structured methods for incorporating inputs from and active participation of SMEs throughout the data analysis lifecycle, from collection and aggregation, through filtering, feature extraction, analysis and optimization.
Some of the challenge will be in just how do we make it easy to gather information from SMEs in real time, while standing in front of equipment in the fab. Internet of Things (Iot) devices are emerging to capture and label images and sounds to enable machine learning algorithms to recognize and help diagnose manufacturing problems based on sight and sound, complementing the instrumented data. But we also need to record the thought processes our human SMEs go through in those investigations – perhaps by the SMEs talking to a smart AI-based conversational assistant who helps make “rounds.” Doing contextual analysis on this added data, combined with the instrumented data, will create the equation Human + Machine = AI (Awesome Insight).
Sounds reasonable, right?
We think artificial intelligence becomes too artificial if you leave the human out of the equation. AI should be augmented intelligence, where we take the expertise and creativity of the human, and combine it with the rapid computational capabilities of the computer, in order to put problem identification and solutions on steroids. But with the already huge advancements to date in data analytics, cloud, and the emergence of AI, why do improvements in quality, machine utilization, and the implementation of predictive analytics in semiconductor manufacturing seem to be creeping along incrementally, and not appearing as dramatic, step-function improvements?
Call it Smart Manufacturing, call it Connected Enterprise, call it Advanced Manufacturing, or Analytics, or Cloud, or the Digital Twin … there are no shortages of terms, philosophies, and technologies available, but why aren’t we seeing their rapid adoption?
It could be it’s the downside that comes with needing people.
“Good business leaders create a vision, articulate the vision, passionately own the vision, and relentlessly drive it to completion.” Jack Welch.
We see from other industries that smart manufacturing conversations originating with the executives of a company thinking to implement smart manufacturing programs lead to vision; however, we also see from other industries, and from our own, that realizing this vision has often been a challenge.
Why is that?
One reason may be that the people who are personally vested in solutions they implemented in the past, as well as those who follow a pattern of ‘how we’ve always done things’, create, inadvertently or not, persistent internal barriers hindering innovative action. Another may be that engagements with the working engineers and managers charged to be smart manufacturing implementers leads to the pursuit of low-hanging fruit, and cautious investments, that often utilize solutions that ultimately cannot scale and integrate.
Not to mention the disadvantage of dealing with the legacy equipment, the legacy networks, the traditional thinking, and the lack of consistency in metrics adding to the confusion. Addressing all these barriers requires an alignment in strategy and execution, along with a plan to support the overall vision, often across the entire enterprise, which is no small matter.
And then there are the standards. Having and adhering to standards in control solutions, networks, and data becomes critical in achieving real benefits from smart manufacturing.
And data security. One of the other big impediments in the smart manufacturing transformation is data and IP security, another key concern (maybe the most significant) preventing us from moving forward more quickly (e.g. to cloud-based solutions) in our industry. More about that in a follow-up.
Achieving synergy across all of manufacturing, from connecting equipment horizontally, through the production system (machines & processes), and vertically, through enterprise systems and across production facilities, can only occur if we build standards, security, infrastructure, and human engagement throughout our ecosystem and supply chain. In simple form, the steps to do so include connecting assets, collecting and contextualizing data, and then driving business transformation with actionable insights gained from the data.
With impact on every function, and every person, in the enterprise, from equipment operators in the fab through the C-Suite in HQ. Maintenance, Engineering, R&D, Operations, Scheduling, IT, Procurement, Finance, HR all contribute, collaborate and benefit. Regardless of the technology, from device level analytics to predictive maintenance and optimization, the people that reside in these disparate groups need to come together with the smart machines to create a common strategy to achieve transformational results.
Aligning an enterprise’s goals with its human capital is paramount to success.
Therefore, we must challenge our team members and ourselves to work outside our comfort zones, and we need to be forever aware of the need for us to grow with the technology. Smart manufacturing is not necessarily about having fewer people in the fab, but it does suggest having people in the fab, perhaps with different, or upgraded, skill sets, who are even more efficient in their roles as a result of the boost they are getting from Industry 4.0.
Fortunately, we now have techniques that let us combine the best, brightest, and latest and greatest analytics with our invaluable SMEs throughout the data analysis lifecycle. We’ll not only be able to deliver higher quality semiconductor manufacturing solutions all in all, but we’ll also be providing methods to more easily distribute, scale, maintain, and continually refine those hard-earned solutions.
We expect that subject matter experts will continue to put the “smart” in machine-based smart manufacturing today, and for the foreseeable future. SME contributions are not an option, but, rather, an imperative for ensuring a semiconductor manufacturer’s sustained prosperity, much less its survival.
Nancy Greco (IBM Watson), Dave Mayewski (Rockwell Automation), James Moyne (University of Michigan / Applied Materials), and Paul Werbaneth (Intevac, Inc.), along with Julie Jacob (Ernst & Young), and Carson Henry (Micron Technology), were members of the SEMI ASMC 2018 panel discussing Industry 4.0 and the Future of Commercial Semiconductor Device Manufacturing. All opinions here are purely our own. Please contact Paul Werbaneth via email at pwerbaneth@intevac.com.
The SEMICON West (July 9-11, 2018, in San Francisco) Smart Manufacturing Pavilion features working production equipment on the floor and three full days of speakers providing insights on building the infrastructure needed to enable AI.
Equipment from Bosch Rexroth, Cimetrix, Rudolph Technologies, INFICON, Final Phase Systems, OMRON, DISCO and Edwards Vacuum will showcase cutting-edge smart manufacturing technologies.
For information on the SEMI Smart Manufacturing initiative and how to get involved, please click here.