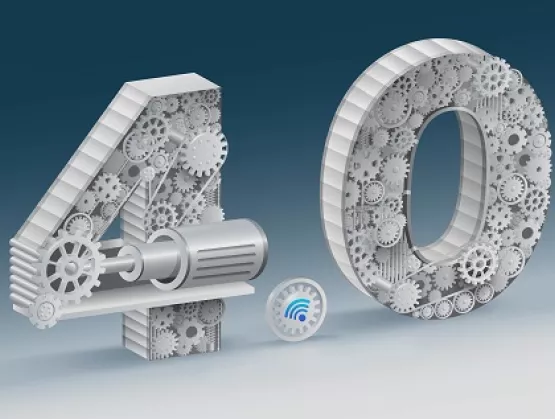
Teck Khiong, WOI, senior manager of Factory Integration at Infineon Technologies Asia Pacific Pte Ltd, recently shared with me how the Infineon backend plant in Singapore has benefited from its journey to qualify for the lighthouse certification.
WOI is driving Infinion smart manufacturing projects with a strong focus in the area of connect and control using IoT (Internet of Things) and analytics technologies.
Ng: How did the Infineon backend plant in Singapore distinguish itself to qualify for lighthouse certification?
WOI: The Infineon Singapore backend manufacturing plant is proud to be a Lighthouse Certified Smart Manufacturing site as part of the World Economic Forum’s (WEF) Fourth Industrial Revolution platform. Our Industry 4.0 (I4.0) implementation reduces labor costs by 30% and improves capital efficiency by 15%. We drove this successful digital transformation continuously investing in our people development and digital backbone.
Of the many initiatives under our I4.0 Smart Factory platform, five were selected for WEF Lighthouse submission and certification.
- Digital foundation with integrated connectivity and workflow execution
We implemented an Internet of Things (IoT) framework to connect machines to manufacturing system more than two years ago. The digitization of our Work-in-Progress (WIP) management systems provides full traceability and gives us better control of the four Ms (Man-Machine-Method-Material).
- Material handling and process automation
We progressively deployed automated solutions starting six years ago using autonomous transport, robotic material management systems and automation of packing processes. This eliminated non-value touches in areas of WIP storage and retrieval.
- Advanced algorithms enabled WIP scheduling and dispatching
As our product mix and volume grew in complexity, our advanced algorithms has enabled us to increase our machine uptime, thus reducing idle and set-up time.
- Manufacturing control tower
Our control tower provides a real-time pulse of the entire manufacturing process, from machine efficiency to quality. The tower also improves data integrity and collaborative information sharing while issuing early-warning alerts that enable exception management and timely decisions.
- Running a global virtual factory
Our Global Production Network deployments allows us to connect and manage a growing contract-manufacturing network in real time, with the same transparency, traceability and control as if the manufacturers are our internal sites.
About Teck Khiong, WOI
Teck Khiong, WOI graduated from Loughborough University in the UK with a Master of Science degree in Computer Integrated Manufacturing (CIM). For more than 20 years he has delivered manufacturing IT solutions to global backend (assembly and test) semiconductor manufacturing, ranging from equipment, factory, process control, material handling automation and manufacturing execution systems (MES).